TECHNOLOGICAL PROCESSES
RIM - pDCPD
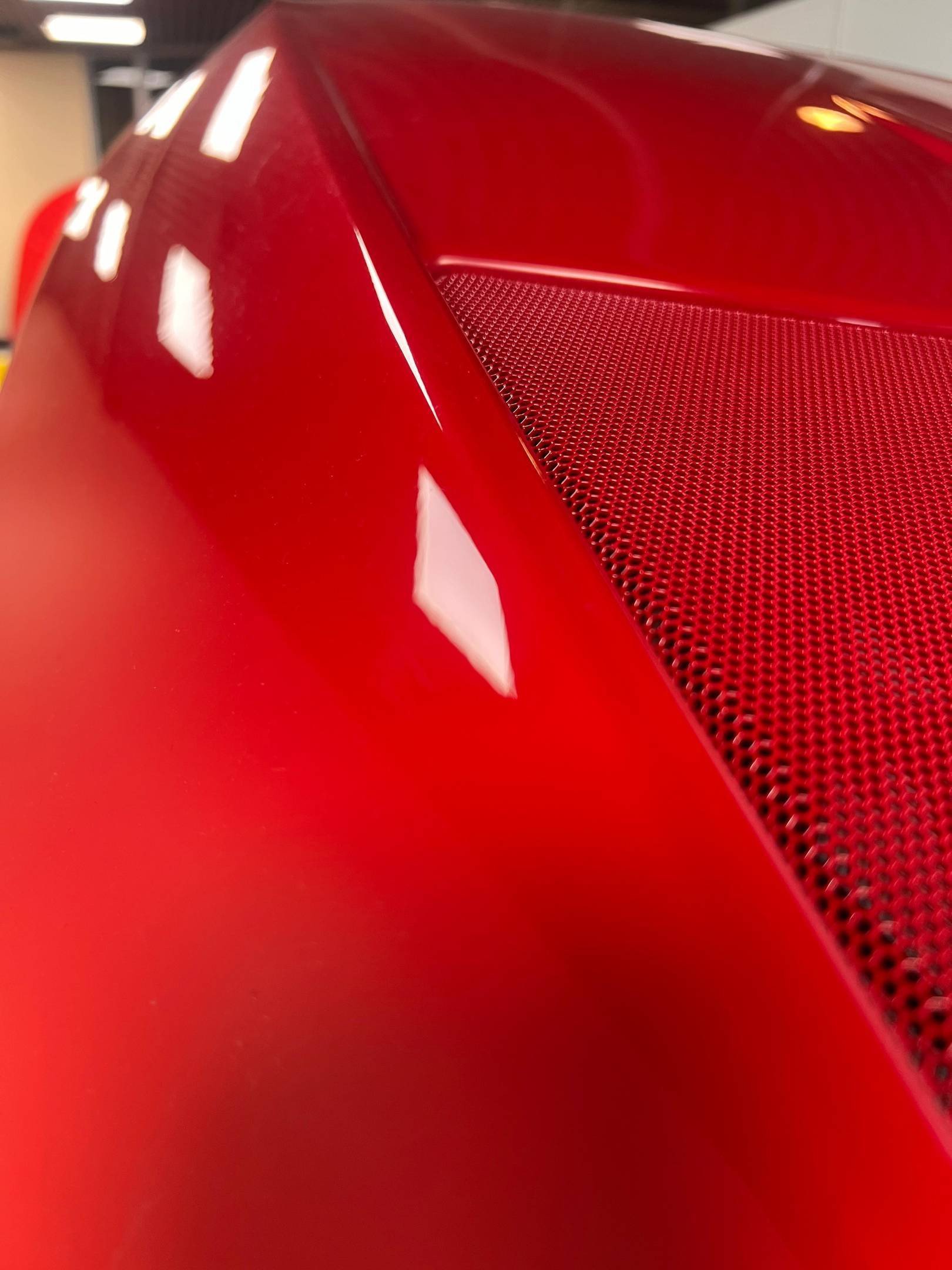
RIM - pDCPD
Polirim uses pDCPD moulded by RIM (Reaction Injection Molding) technology,
to offer a series of advantages to a wide range of industrial applications.
Its main characteristics are:
• Optimal balance between resilience and stiffness: PDCPD provides an excellent balance between flexibility and robustness
• High impact resistance even at low temperatures: it maintains its structural integrity and functionality even in extreme thermal conditions -40° <T<130°
• Excellent resistance to chemical agents: effectively resists the corrosive action of many chemical substances, prolonging the life of the components made
• Dimensional stability: guarantees precision and reliability over time
• Low specific weight: with a low weight, it is ideal for applications where weight is a critical factor
• Fast Production Cycles: RIM technology enables fast production cycles, increasing efficiency and reducing cost.
• Excellent surface quality and easy paintability: PDCPD guarantees a high level of paintability
• Aluminum moulds: guarantee precision, lightness and durability, helping to reduce costs and time to market
• Low environmental impact and energy consumption molding: our processes are designed to be environmentally sustainable, minimizing energy use and reducing the carbon footprint
to offer a series of advantages to a wide range of industrial applications.
Its main characteristics are:
• Optimal balance between resilience and stiffness: PDCPD provides an excellent balance between flexibility and robustness
• High impact resistance even at low temperatures: it maintains its structural integrity and functionality even in extreme thermal conditions -40° <T<130°
• Excellent resistance to chemical agents: effectively resists the corrosive action of many chemical substances, prolonging the life of the components made
• Dimensional stability: guarantees precision and reliability over time
• Low specific weight: with a low weight, it is ideal for applications where weight is a critical factor
• Fast Production Cycles: RIM technology enables fast production cycles, increasing efficiency and reducing cost.
• Excellent surface quality and easy paintability: PDCPD guarantees a high level of paintability
• Aluminum moulds: guarantee precision, lightness and durability, helping to reduce costs and time to market
• Low environmental impact and energy consumption molding: our processes are designed to be environmentally sustainable, minimizing energy use and reducing the carbon footprint
RIM - PU
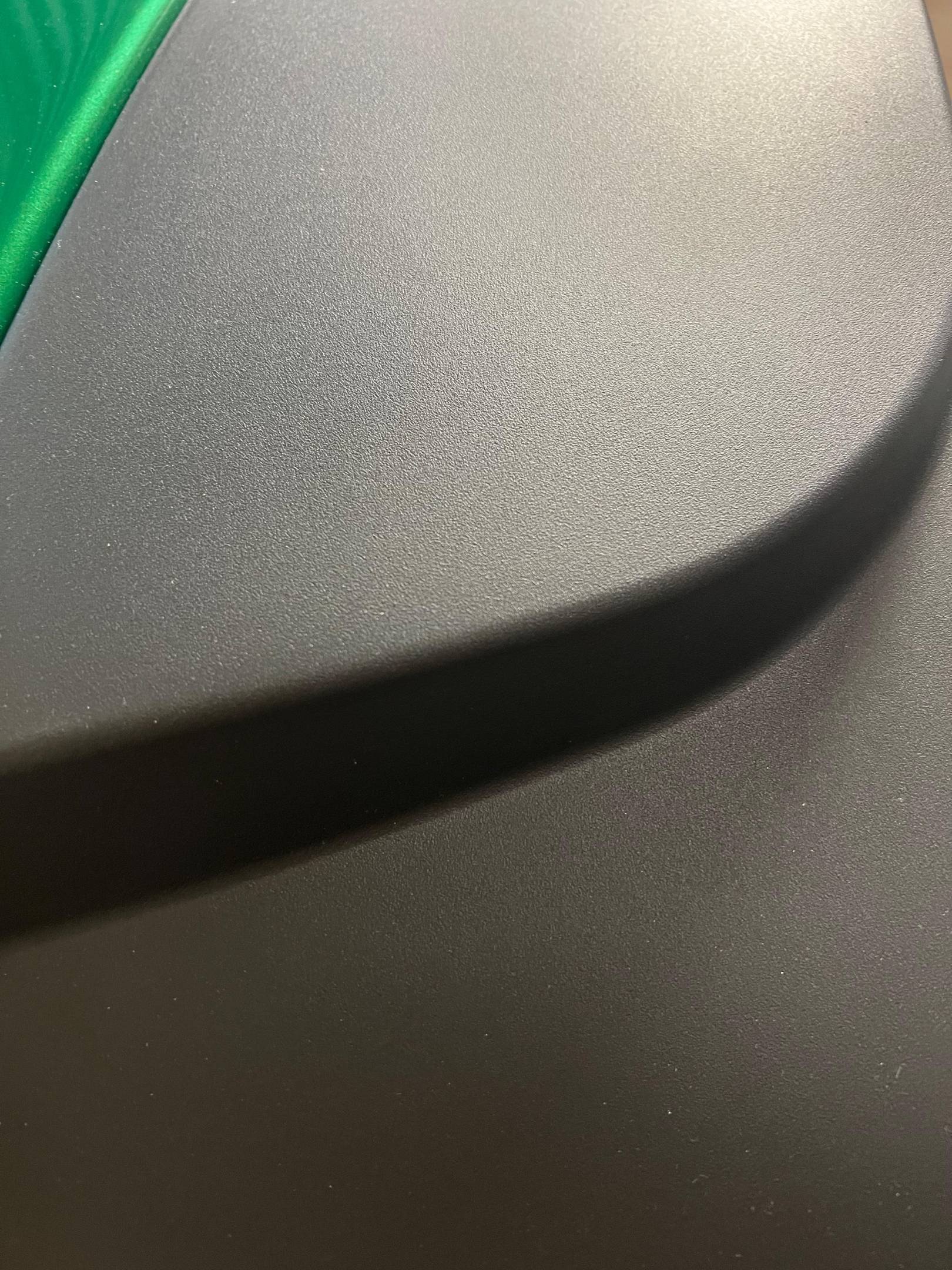
RIM - PU
RIM-PU technology is at the forefront of the elastomeric polymer sector.
Here are the main characteristics of this extraordinary material:
• Elastomeric polymer with high mechanical characteristics: guarantees excellent performance in applications that require resistance and durability
• Elongation at break of 200%: offers considerable elasticity, allowing the material to stretch without breaking, ideal for dynamic applications
• Dimensional stability: maintains its size and shape even under stress and temperature variations, ensuring precision and reliability in the final products
• Impact resistance: Designed to absorb and dissipate energy, protecting components and improving product longevity
• Mass black coloring: integrated coloring ensures a uniform appearance and greater resistance to scratches and wear, reducing the need for additional surface finishes
• Excellent surface quality: the material finishing is uniform and can be textured in mold improving the aesthetics of the final product
• Aluminum Molds: We use high-quality aluminum molds that offer precision and repeatability, contributing to efficient manufacturing processes and high-quality results
Sheet Moulding Compound
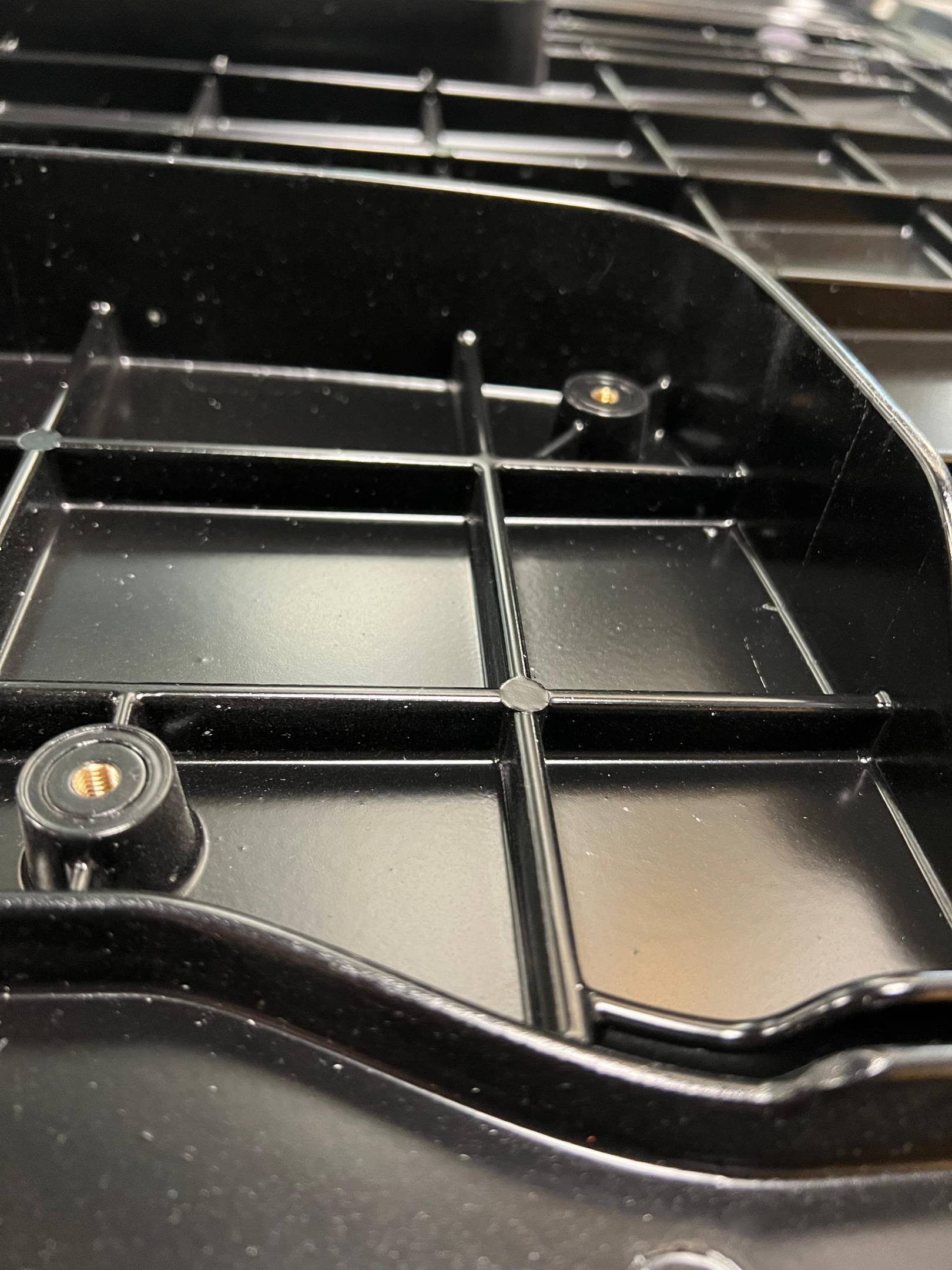
Sheet Moulding Compound
Our compression molding process uses thermosetting polyester resin reinforced with glass fiber, a material that guarantees excellent mechanical and resistance characteristics.
Below are some of the main qualities of our product:
• Strength and dimensional stability: our thermosetting polyester resin, reinforced with glass fiber, ensures superior dimensional stability, maintaining the original shape and dimensions even under extreme mechanical loads
• High rigidity and resilience: The material offers considerable rigidity and resilience, making it ideal for applications requiring strength and durability. These properties allow the products to resist shock and stress without deforming
• High temperature resistance: Designed to operate in high temperature environments, our products can withstand temperatures up to 200°C. This makes them perfect for industrial applications in severe thermal conditions
• High quality molds: we use chromed steel molds, ideal for large-scale production. The chrome plating of the molds guarantees durability and precision in the molding process, ensuring an extended life cycle and constant quality of the final product
Injection Moulding - Thermoplastic
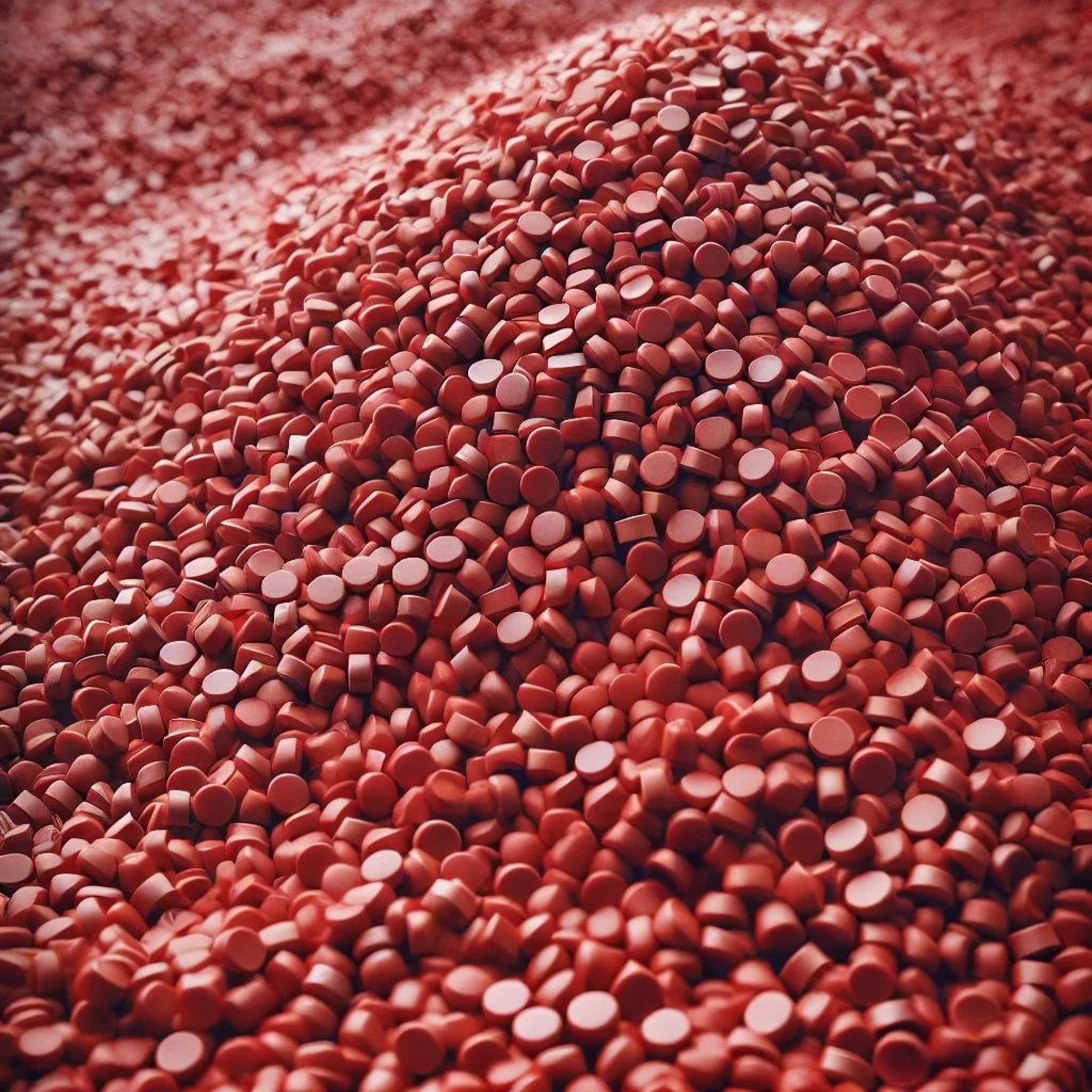
Injection Moulding - Thermoplastic
Polirim offers high quality solutions for a wide range of industrial applications. Our injection process is optimized to ensure maximum precision and product durability, using a variety of advanced thermoplastic materials.
Used materials:
• ABS (Acrylonitrile Butadiene Styrene): a versatile and resistant polymer, ideal for applications requiring high rigidity and dimensional stability
• PC-ABS (Polycarbonate-Acrylonitrile Butadiene Styrene): combines the properties of PC and ABS to offer an excellent balance of strength, impact resistance and machining ability
• ASA (Acrylonitrile Styrene Acrylate): characterized by excellent resistance to atmospheric agents and color stability, it is perfect for external applications
• PA6 (Polyamide 6) with glass fibre: offers high mechanical and thermal properties, suitable for components requiring high strength and rigidity
• PP (Polypropylene): known for its lightness and chemical resistance, it is widely used in many industrial sectors
• PP-EPDM (Polypropylene-Ethyl Propylene Diene Monomer): a combination that gives the material excellent elasticity and resistance to aging
Used materials:
• ABS (Acrylonitrile Butadiene Styrene): a versatile and resistant polymer, ideal for applications requiring high rigidity and dimensional stability
• PC-ABS (Polycarbonate-Acrylonitrile Butadiene Styrene): combines the properties of PC and ABS to offer an excellent balance of strength, impact resistance and machining ability
• ASA (Acrylonitrile Styrene Acrylate): characterized by excellent resistance to atmospheric agents and color stability, it is perfect for external applications
• PA6 (Polyamide 6) with glass fibre: offers high mechanical and thermal properties, suitable for components requiring high strength and rigidity
• PP (Polypropylene): known for its lightness and chemical resistance, it is widely used in many industrial sectors
• PP-EPDM (Polypropylene-Ethyl Propylene Diene Monomer): a combination that gives the material excellent elasticity and resistance to aging